The die casting is a process in which the metal is cast defined by forcing the molten metal under high pressure into a mold cavity. Most die castings are created using hard metal dies and are usually made of non-ferrous metals such as aluminum. Die casting China is identified by a reliable surface coating and shine by casting standards and consistency. Die casting is usually used where you require parts or tools that are stable and durable.
Die casting is a reasonable yet reliable method of forming a wide variety of shapes. It is thought about beyond numerous producing techniques and is considered as sturdy, combining seamlessly with the multiple parts of the equipment of which it belongs. Die casting has lots of advantages and chief amongst them is its potential to render complex shapes with a high degree of tolerance.
A high-pressure die casting is a fabrication process in which the aluminum in its liquified form is infused with casting equipment under the ultimate high-pressure rate into steel or mold, to create parts of the desired shape and style. The size of the equipment ranges from 400 to 4000 loads.
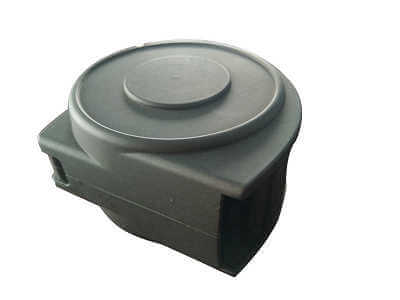
Aluminum Die Casting
The factor for the expanding popularity of the aluminum die-casting sector is for its light-weight as well as anti-corrosion attributes. Employed in multiple applications aluminum die castings are economical in nature and significantly cater to the need of users. Apart from that, this metal has high dimensional stability for complex designs. High thermal and electric conductivity, in addition to the ability to endure high temperatures, has actually made aluminum a great source for high-pressure die casting, a much-preferred option nowadays.
Die casting aluminum nowadays has improved a lot and have actually rightly replaced computerized quality assurance. Today there are several types of tools utilized in the die casting method, which can make your work convenient, saves time and increase efficiency. While some die-casters use various tools to oil dies, ladle metal into cold chambers others utilize them to incorporate various other functions like quenching.
This technology is marked for its high-quality utilitarian parts. It is used in making tools, equipment, and parts of electronic devices like digital cameras, smartphones, and MP3 players among others.
Lightweight aluminum die casting is understood for creating precision parts. While making sure of good surface finish they get rid of the requirement of post-machining. Produced under the strict guidance of experts, die-casting aluminum components assure impeccability as well as comply with the International Standards.
Lightweight Die Casting Aluminum is used in a number of industries as it is marked high quality and exceptional characteristic. The process ensures efficiency and productivity as well as is recommended for its authenticity and durability.
CN Manufacture Tech (CNM TECH CO.LTD) is an aluminum die casting manufacturer located in China dealing in various other die casting products, machining parts, and injection-molded parts as well. Our team of professional designers and manufacturers are always eager to take on new projects. For more deeds, visit our official website.